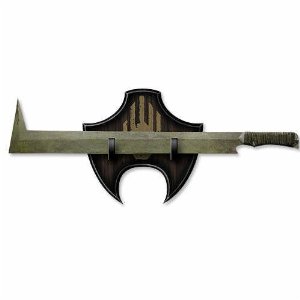 |
*Reference photo from Amazon.com |
Pesky Hobbits are no match for me!
I had my eye set on this set of replica swords from the Lord of the Rings movies. You can buy them online, but they are very expensive. They have recently dropped in price but are still at least $100 and up to around $300. The one I really wanted was that gnarly sword the orc's use. The one that looks like a big machete with a spike on on the end. It was cool but $100?
This was going to be my first prop building project. Something nice and simple so I didn't get discouraged. I started out by searching for all the reference material I could find. It wasn't too hard because you can actually order one of these swords. The problem was picking out the design I wanted. There was the "official version" the one created by the Weta team, and some unofficial knock-off's floating around on the web.
I came up with a design that was as true to the movies as I could get it and drafted it in Photoshop.
I traced the image I printed on some carbon paper and cut it out with a Jig Saw (a Band Saw would have worked better but I don't have one). My design is three pieces. The blade and the handle in two sections to fit on either side to get the full tang look.
Sharpening the blade was a little tricky. I used a belt sander to grind down the wood, but had a hard time getting a clean edge. I also sanded the edges of the handles to round them a bit.
I had no experience painting anything like this. I put a couple coats of primer on and then used a "hammered finish" metal spray paint for the blade. I was hoping for something with more texture, but the paint came out finer than I wanted. I used acrylic pant for the handle and dabbed some on the blade to look like rust.
Challenges:
I used .25" MDF board for this project because it is cheap and easy to work with, but I might have been better off with Pine, or some other non-composite board. The MDF is really brittle at the thin parts of the bade and has chipped and broke a few times while I was building this. I do like that it has a bit of flex to it so it bends like an actual blade would.
How to paint wood to look like rusted hammered metal? I'm still working on that.
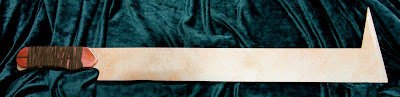 |
Here is the finished sword |
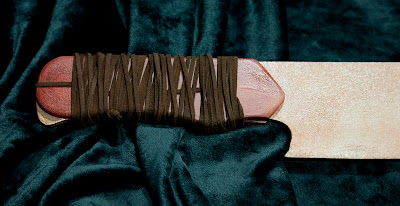 |
A close up on the handle |
This was a great first project for me. It wasn't too complicated and I am pretty happy with how it turned out. I'm looking forward to starting the next project.
Here are some of the tools and materials I used for sale on Amazon.com
*Some of these are not the exact product but comparable to what I used.